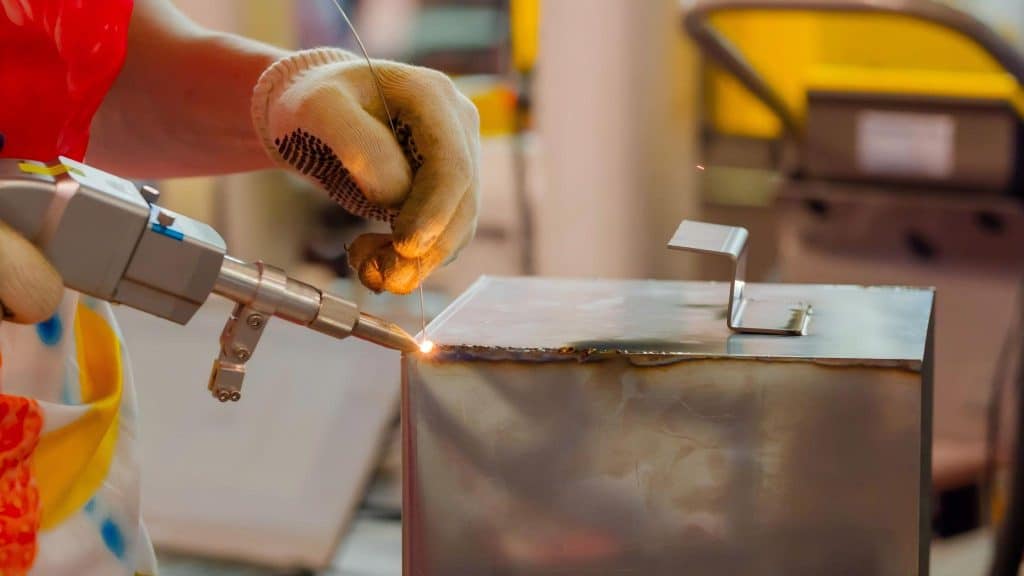
To achieve high-quality and consistent welds, the welder needs a “weld fixture”, a specialized jig or tool that holds and supports the workpieces.
With a weld fixture, high-volume manufacturers can easily align metals. This alignment ensures the production of robust welds, fast-tracks the welding process, and minimizes material distortion.
In this article, we discuss four common types of welding fixtures and their benefits to traditional MIG/TIG setups and modern laser welding applications.
What Is a Welding Fixture?
A welding fixture is a stable tool or platform that holds and secures workpieces. It is crucial to maintain the workpieces in correct orientation and facilitate consistent and accurate weld placement. Using a welding fixture often ensures superior weld quality with minimal distortion.
Welding fixtures are also important for quick and efficient production repeatability. They ensure that each weld is made under the same conditions, positions, or orientations without the need for readjustment or realignment.
And since fixtures prevent material movement during welding, they lower the risk of accidents caused by an unstable setup or sudden shift of the workpieces.
Traditional MIG and TIG setups often use fixtures to hold the metals and maintain consistent gaps. But even modern techniques with higher precision levels still rely on fixtures to achieve clean welds. For instance, Denaliweld’s Jet 1000 and Cobot Series, which are lightweight and automation-ready laser welding machines, can operate continuously in a wide temperature range of -10°C to 40°C with a high-quality welding fixture.
4 Types of Welding Fixtures You Need to Know
The success of a welding project often relies on the type of welding fixture used. Get to know the most common types of fixtures in this section.
Manual Welding Fixtures
From the name itself, this type of fixture relies on the welder’s manual operation to work. No automated or powered assistance is involved with manual welding fixtures.
These fixtures are simple and cost-effective as they only utilize toggle clamps, jigs, and set screws. These components are usually easy to adjust between welding operations.
Manual welding fixtures are typically applied in small batch production, prototyping, or low-volume production. They also work well with high-quality handheld systems, such as Denaliweld’s Air-Cooled Laser Welding Machine, which are often used in projects that require high attention to detail or less dependence on the operator’s skills.
Semi-Automatic Welding Fixtures
A semi-automatic fixture uses hydraulic actuators (usually activated by a switch or foot pedal) or pneumatic systems to align workpieces. It is typically used in repetitive, medium-sized productions where a good balance between speed and flexibility is required.
In this weld fixture type, the operator is still the one controlling the welding process. However, the fixture automates the metal positioning and handling.
Modern laser welding equipment, such as Denaliweld’s water-cooled laser welding machines, uses semi-automatic welding fixtures for continuous-duty cycles in which the same parts are meticulously fused during the day.
Fully Automatic Welding Fixtures
For projects that require minimal human intervention but high repeatability, a fully automated fixture integrated into a robotic, CNC, or mechanized welding system is ideal.
This type of fixture uses a programmed control system, clamping sequences, and sensors to hold the workpieces. It can also follow algorithms to match a client’s technical requirements. Some even feature advanced verification systems to detect metal misalignments and adjust them prior to the welding process.
Most high-volume production lines use fully automatic welding fixtures because they handle tasks significantly faster than manual welding fixtures. They can reduce welding cycle times or easily scale production up or down based on demand without significant changes to the setup
Modular Welding Fixtures
A modular welding fixture is a flexible system that can be reconfigured easily for shifting production demands. It often uses grid-patterned base plates and clamping pieces that can be adjusted or reassembled to meet new project requirements. Hence, this type of fixture is commonly applied in prototyping and custom fabrication shops.
Choosing the Right Welding Fixture for Your Project
Upon recognition of common weld fixture types, it is time to choose which one fits your project needs. Here are some relevant factors to consider:
- Workpiece Material Type: Since different workpieces respond to heat differently, you need to ensure that the fixture can adequately withstand material thermal contraction or expansion caused by heat application. Moreover, the fixture must be strong enough to support the workpieces in place during the welding process.
- Part Complexity: The fixture design must be appropriate to the expected geometry of the end product. It must be compatible with the workpieces’ dimensions and geometric features to maintain consistent alignment throughout the welding process.
- Welding Method: TIG and MIG are usually done with a manual welding fixture that enables precise control over the welding arc. Meanwhile, modern methods such as laser welding are best paired with semi-automated or fully automated welding fixtures to match their high-level precision and speed.
- Production Volume: Simple manual fixtures are best for low-volume production because they are cost-effective and straightforward. But for high-volume production lines, an automated fixture is preferred. For projects that require complex design or configuration, a module welding fixture might be necessary.
Applications and Use Cases for Welding Fixtures
Listed below are some common applications of welding fixtures.
Automotive frames and chassis: Fixtures help in the production of robust and error-free frames, body panels, and engine parts.
Aerospace assemblies: Precise and reliable welds are crucial in the aerospace industry. So, fixtures are a must-have in its welding process. High-quality turbine blades, fuselage sections, and hydraulic systems are made possible with a fully automated welding fixture.
Sheet metal fabrication: A fixture that can handle metals with different specific heat and inherent metallurgical properties ensures seamless assembly of flat metal sheets into different structures.
Electronics: Ultra-precision is required to prevent damage to electronic components during welding. Fixtures can support these components throughout the welding process for optimal output.
Step Up Production With High Quality Weld Fixtures and Welding Equipment
For critical applications that require durable, reliable, and clean welds, the workpieces to be welded must be held and supported properly. This is only possible with a weld fixture.
A weld fixture may be operated with human intervention (manual welding fixtures) or through automated systems. It is important to choose the right fixture type for your project to ensure high-quality welds.
More importantly, your welding equipment must come with innovative features for an efficient, stable, and cost-effective welding process. Denaliweld offers cutting-edge laser welding solutions across the US, Europe, and Asia. Our machines are CE/SGS/WPQR-certified, designed by reputable laser industry professionals, and equipped with sophisticated control systems and laser sources.
From the automotive and aerospace industries to electronic and consumer manufacturing, Denaliweld strives to offer laser welding machines for optimal industrial production.