Introduction
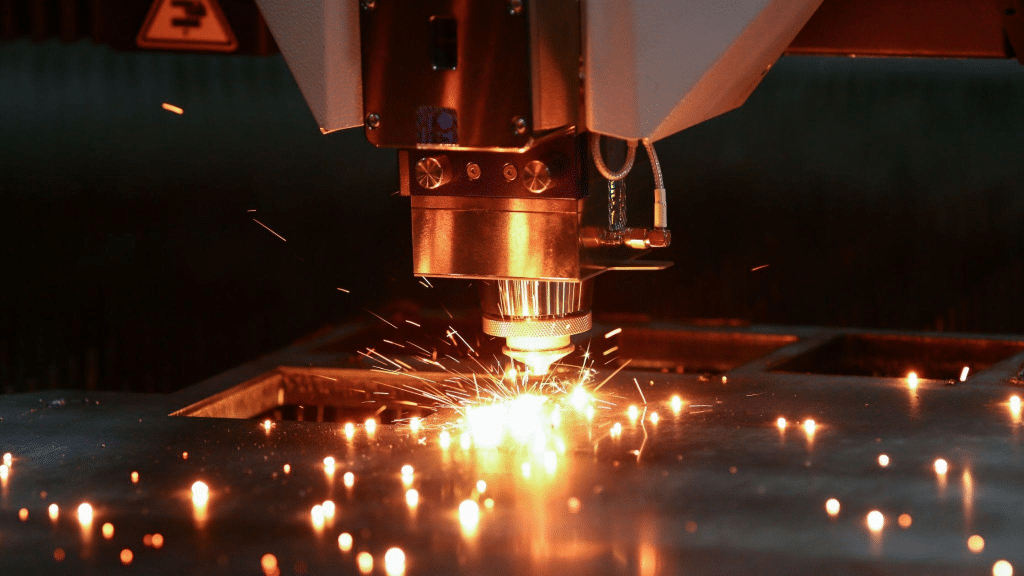
Laser welding has gained immense prominence among modern industries for good reasons. Its efficiency and precision are spot on, and it’s much stronger than MIG or TIG.
Yet, when people assert laser welding strength, it’s often based on subjective assessments or experience. An objective and reliable method to measure laser weld strength is crucial to ensure product quality, safety, and integrity.
In this article, we discuss tests and procedures that will help you evaluate laser weld strength with utmost accuracy.
Why Does It Matter to Test Laser Weld Strength?
Adequate laser weld strength ensures the welded joints withstand tension, stress, or load. This condition ensures that the product (containing the welds) is durable and safe for industrial or commercial use.
Upon material fusion, manufacturers must test the strength of the bond created by laser welding as part of their quality and safety evaluations. Physical tests like Tensile or Impact Testing are necessary to accurately measure laser weld strength. Failure to satisfy these tests may necessitate a redoing of the laser welding process.
Key Factors Affecting Laser Weld Strength and Integrity
When operators address queries like “Is laser welding strong?”, they also check the factors listed below aside from performing physical tests.
- Material Properties: Materials with high absorption rates, low reflectivity, low thermal points, and high specific heat often produce strong laser welds with minimal thermal distortion. Generally, laser welding works well with metals (e.g. aluminum, brass, copper, steel).
- Welding Parameters: A laser welding machine parameters set in an optimal condition produce high-quality welds. Crucial parameters include laser power (in Watts), penetration speed, and focus.
- Joint Design: The inherent design of the joints may also affect laser weld strength. For instance, butt and lap joints in laser welding are typically strong and durable because their structure enables direct fusion of the pieces’ ends.
- Environmental Conditions: Minimal atmospheric contaminants in the welding environment limit distortion in the weld area. The use of a shielding gas in conjunction with laser welding may also influence weld strength.
How Strong is Laser Welding: Effective Methods to Evaluate Strength
Tensile Testing
In this test, controlled tension is applied to determine the maximum amount of force that the laser-welded joint can withstand until it breaks.
To perform this test, the joint is placed between two fixtures or grips that clamp it. Then, weight is applied to the material gripped at one end while the other end is fixed. The force or weight is increased gradually while yield or tensile strength is measured until the joint breaks.
Bend Testing
Commonly used in laser welded butt joints, the bend test measures the joint’s maximum ductility and angle of deflection (i.e. amount of bounding) when bending force is applied.
A mechanical or hydraulic machine is needed for bend testing. It has adjustable clamps that hold the welding specimen and a dial gauge that estimates the joint’s deformation during the application of force. The tester will check the quantitative curvature score and look for cracks or dents to infer the strength of the laser weld.
Impact Testing
This test determines the welded joint’s shock absorption and resistance when hit by a high-impact force. It shows whether the specimen remains intact in the face of a sudden force. To perform this test, a hammer or pendulum strikes the specimen and a measuring device estimates the amount of energy absorbed (in Joules).
The tester must correctly set the environment’s temperature to get a precise measurement from the impact test. Depending on the specimen’s material type, the impact test is conducted from -196°C up to room temperature.
Hardness Testing
The International Organization for Standardization (ISO) specified the Vickers and Knoop tests as the “gold standards” to estimate a laser weld’s resistance against indentation accurately.
In the Vickers test, a squat pyramid indenter is pressed against the specimen for 10 seconds. Afterward, the tester measures the length of the diagonals formed to calculate the indentation damage induced. The Knoop test works in the same manner as the Vickers test, except that it uses an elongated-shape indenter.
The Vickers test is more destructive between the two because it penetrates the material deeper. So, materials with coating thickness below 60 microns must be tested with the Knoop test.
Ultrasonic Testing
This non-destructive strength test uses high-frequency ultrasound waves to check for cracks, discontinuities, or unwanted foreign materials in the welded joints.
To perform this test, a specialized machine called the transducer converts electrical energy into short pulse waves with frequencies from 0.1 to 15 MHz. The transducer transmits these sound waves into the material via a coupling medium (e.g. oil or gel).
The ultrasound waves propagate around the material. But when they encounter boundaries or imperfections, they “bounce back” and are recorded by a flaw detector.
Radiographic Testing
Radiographic testing is also a non-destructive test that uses X-rays or Gamma rays to catch internal structural imperfections in the laser welded joints.
In this test, the specimen is placed between a radiation source and film (or a digital detector). When the radiation passes the specimen, the film or detector produces an image of the material’s internal structure through a contrast based on density and thickness. This will reveal any cracks or imperfections within the weld.
Expert-Recommended Strategies for Stronger Laser Welds
Here are some foolproof measures to achieve high-strength laser welds:
- Use the appropriate laser power according to the material’s thickness and specific heat.
- Maintain an optimized welding speed to prevent excessive heat input that may compromise the material’s quality.
- Use a shielding gas like Argon or Helium to isolate the weld from external contaminants that may cause unwanted chemical reactions.
- Choose the correct joint design according to the product or application you are trying to achieve. Make sure that the components align correctly to prevent gaps in the weld.
How Strong Are Laser Welds: DenaliWeld’s Clear-Cut Answer
With the correct procedure and a high-quality machine, laser welds can easily pass strength tests that measure resistance against tension, impact, bend, and internal impurities.
Achieve laser welds with superior strength with Denaliweld’s top-notch laser welding solutions. We are a global manufacturer of laser welding machines formulated by top engineers and designers in the laser industry. Uplevel your production speed and efficiency with our in-house, innovative designs for laser sources and control systems. Visit DenaliWeld today.