Introduction
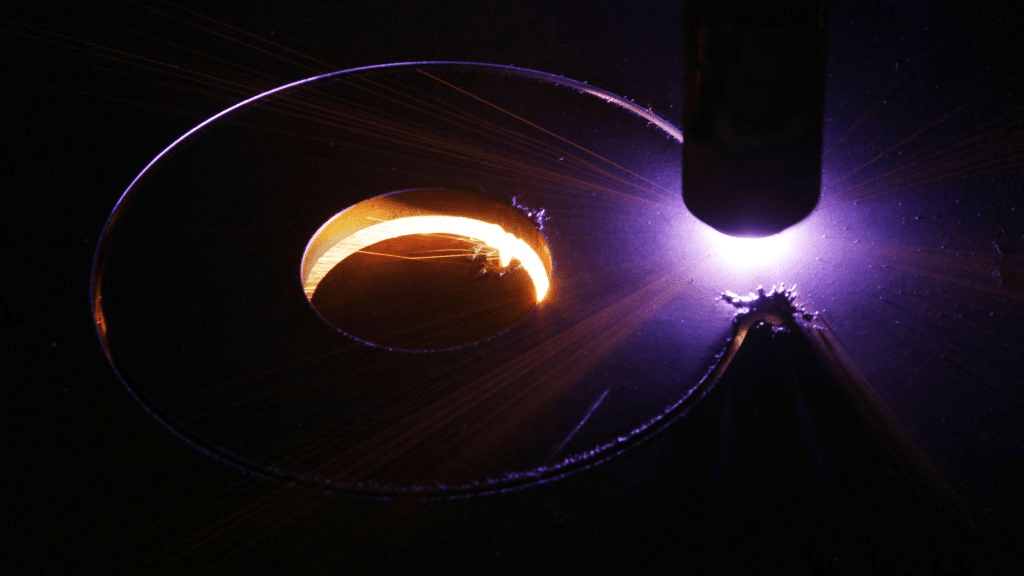
For many years, welders have relied on the metal inert gas (MIG) welding method to heat and fuse workpieces. However, manufacturers eventually shifted to laser welding since its invention in the early 1960s. Many claim that laser welds are superior in strength compared to MIG welds.
But is there any truth to these claims? We examine industrial facts and data, comparing laser welding and MIG welding in terms of strength, precision, efficiency, and application. Our verdict is presented in this article.
What are MIG Welding and Laser Welding?
MIG welding employs an electrical power supply to fuse metal workpieces with an electrode filler that is continuously fed to the welding torch. With an experienced welder, MIG welding easily works with thick materials positioned either horizontally or vertically.
On the other hand, laser welding utilizes high-powered laser beams to heat the workpieces. When the material reaches its melting point, a molten pool is created. A strong weld forms upon the solidification of this pool.
A strong weld is formed when the molten pool solidifies. Unlike traditional methods, laser welding does not create an electric arc to join materials.
Both MIG and laser welding methods use shielding gases such as Argon, Nitrogen, or Helium to protect the weld from external factors contaminants.
Is Laser Welding Stronger Than MIG Welding?
In general, laser welding is stronger than MIG welding. And when we say “stronger”, it means that laser welding beats MIG in terms of penetration, metallurgical bonding, and speed.
Penetration
Even with a single pass, the high-density focused beam of laser welding causes localized material vaporization and penetration of about 1 to 12 millimeters (Denaliweld CR4000w/Trident 6000W laser welder). This impressive penetrating capacity is due to the machine’s ability to concentrate the laser beam on a specific spot. This concentration results in deep and narrow welds with a high aspect ratio.
In contrast, MIG welding spreads heat over a larger area, limiting the arc’s ability to penetrate a specific spot. Consequently, MIG welds, even at high energy levels, are generally wider and shallower compared to laser welding.
Speed and Efficiency
In MIG welding, the operator must feed filler material into the weld pool. It’s a tedious and time-consuming process that makes MIG slower than laser welding, as the latter melts the material directly without filler material.
Laser welding is about three to ten times faster than MIG welding, thanks to its high-intensity, concentrated beam that penetrates even thick materials in just a few seconds.
Laser welding can penetrate medium to thick materials at impressive speeds of up to 0.8 inches per sec.
Metallurgical Bond
Bonds formed by laser welding are usually better than ones by MIG. This is because of laser welding’s ultra-concentrated heat input that effectively refines the fusion zone’s microstructure. And since laser welding does not rely on a filler material, the metallurgical bond remains pure and homogeneous. So, the weld’s strength is almost equivalent to the parent material’s inherent strength.
The strength advantage of laser welder vs MIG highly depends as well on the performance of the laser welding machine.
For instance, Denaliweld’s Water-Cooled Laser Welding Machine provides better laser welding performance compared to MIG welding. It generates up to 4000w output for strong and precise welds with minimal distortion. It’s also equipped with an intuitive laser control system to produce a smooth output curve at a safe temperature range. Our machines are also smaller in size for easy laser position adjustment and energy conservation.
Precision & Heat Control: How Do Laser and MIG Welding Compare?
Heat application in laser welding is more focused and precise, so it ensures a smaller heat-affected zone (HAZ) and minimizes thermal distortion.
Many laser welding machines also utilize specialized software and controls to adjust the beam’s center for an optimal HAZ area. So, even beginner welders can easily maneuver the machine and redirect the beam while maintaining the laser beam’s precision.
Meanwhile, heat applied by MIG welding is usually distributed to a larger area compared to laser welding. This distribution makes a MIG weld prone to material distortion.
Is Laser Welding More Cost-Efficient Than MIG?
As discussed above, laser welding is faster than MIG welding. Hence, laser welding produces welds at a higher volume at a faster rate. This significantly reduces operating costs.
And since laser welding minimizes thermal distortion, post-welding corrections or refinements are not needed. This saves time and resources and improves the manufacturer’s overall production performance.
Which One is More Versatile?
Both welding techniques are versatile. But as most industries strive for better weld quality and faster production processes, laser welding has gradually taken over MIG’s spot as the most favored method.
For instance, in the automotive industry, laser welding is vital to creating high-integrity vehicle body panels as this method ensures minimal material distortion. It also creates strong and lightweight joints that contribute to a vehicle’s fuel efficiency and longevity. MIG welding is still widely used in this industry but is typically used only when filler materials are necessary to fill gaps in case of a poor fit.
Laser Welding vs. MIG Welding: The Clear Winner
Laser welding fares better than the traditional MIG method with its stronger heat input, precise application, and minimized heat-affected zone. It also speeds up the production process, drives operating costs down, and works well with multiple modern industries.
To achieve laser welding’s full potential, invest in a high-precision fiber laser welding machine such as from Denaliweld. We are a leading global provider of laser welding solutions engineered with the highest standards in terms of strength, safety, and quality. Our machines are all CE/SGS/WPQR-certified and made with leading-edge proprietary technology with unmatched precision and power.