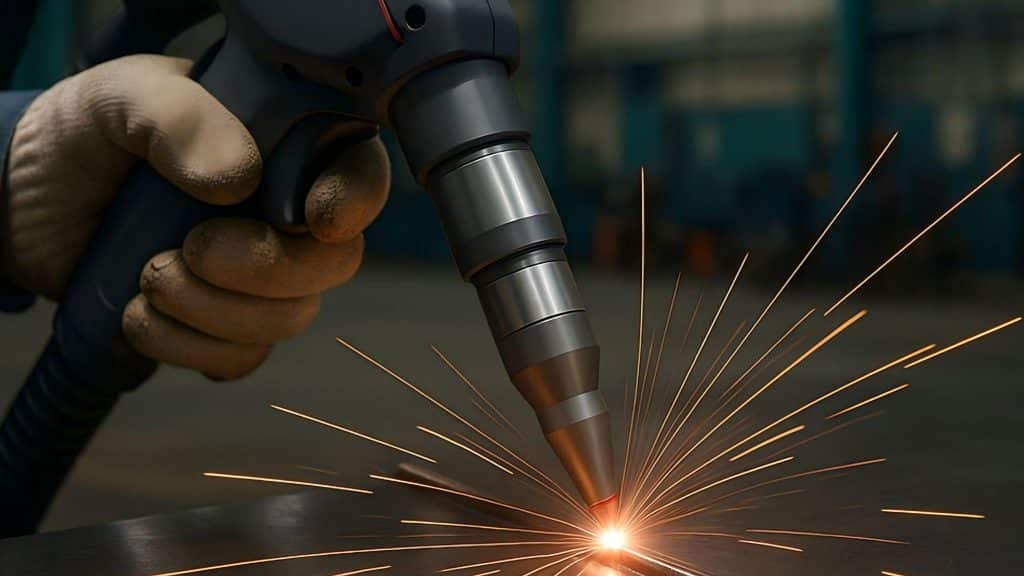
As with other welding techniques, laser welding is a process that requires more than just a machine. This craft entails a complete, effective, and standard-compliant system that every manufacturer must be familiar with. For instance, certain parameters must be optimized and several principles must be considered for successful laser welding.
In this blog, we outline the most essential laser welding requirements for a high-quality and reliable weld.
What Are the Parameters of Laser Welding?
In laser welding, several interrelated parameters are at play to influence weld quality. Familiarity with these parameters is essential to achieve a precise, high-quality weld that is reliable in any industrial application.
Here are the common laser welding parameters that must be fine-tuned for optimal weld performance:
1. Laser Power
Laser power determines the amount of energy supplied to the workpieces. Power and welding penetration is directly proportional (i.e. higher power increases penetration depth and heat input). Hence, a more powerful laser enables deeper and stronger weld.
However, excessive power can lead to defects such as spatter or burn-through. Some metals melt excessively and turn unstable when excessive heat is applied. This results in larger molten metal droplets being expelled from the weld pool.
2. Laser Welding Speed
In welding, speed pertains to the rate at which the heat source moves along or penetrates the workpiece. At higher rates, heat input is lower, which results in narrower welds and shallower penetration. On the contrary, slower rates induce greater heat absorption, which translates to larger heat-affected zones (HAZ).
Typically, thicker metals like mild and stainless steel, need slower speeds to avoid burn-through and achieve proper welding or fusion. Meanwhile, thinner materials, such as aluminum, require higher welding speed so they won’t absorb much heat and avoid unwanted material melting.
3. Focal Position
The laser welder’s focal point is the location where the laser beam converges and concentrates its heat and energy. If the laser’s focal point is positioned right below the material’s surface, the penetration depth increases. Meanwhile, a focal point positioned above the surface results in wider but shallower welds and joints.
4. Laser Classification
Laser welding has two forms: pulse and continuous.
In pulsed mode, energy is delivered in short, controlled bursts, which minimizes heat input and is ideal for thin or delicate materials. On the other hand, the continuous laser mode generates a steady and uninterrupted beam of energy that is suitable when working with thicker base materials that require consistent energy input for a cleaner and stronger weld.
5. Laser Beam Size
The laser beam’s diameter affects the laser welder’s energy density, or the amount of heat and energy applied in a particular spot. Mathematically, energy density is inversely proportional to the square of the beam’s diameter. This means that a smaller diameter translates to stronger and more concentrated laser beams.
For instance, a smaller beam, such as one that is around 0.4 mm, generates high laser energy density, which efficiently penetrates deep and thick surfaces. When welding stainless steel plates of 3 mm thickness, a narrow beam can focus sufficient energy to melt the material deeply and create a strong joint with minimal surface deformation.
On the other hand, a larger beam, which is at least 1.5 mm, can deliver lower energy density. This beam size works well on thin materials like aluminum sheets. Since larger beams translate to less dense energy application, it reduces the risk of excessive heat and energy application that may cause material distortion.
What PPE Is Required for Laser Welding?
High-intensity laser beams can cause skin burns, eye damage, or inhalation of harmful fumes. For this reason, a laser welding operator must wear personal protective equipment (PPE) to meet laser welding safety requirements.
Here are some required laser welding PPE:
- Safety glasses or goggles: Even indirect laser beam reflection can cause irreversible eye damage or retinal damage. So, it is important to wear protective glasses or goggles during welding operations. Note that protective glasses must be specific to the laser wavelength being used (e.g., 1064 nm for Nd: YAG lasers or 10.6 µm for CO₂ lasers). And as much as possible, the glass must satisfy the ANSI Z136.1 or EN 207 standards for laser safety.
- Protective gloves: Since the operator’s hands are close to the welding zone, they are highly vulnerable to cuts and burns. For this reason, you need durable, flexible, flame-resistant, and comfortable gloves that will protect your hands during the operation. Common glove materials used in laser welding include Kevlar and leather.
- Anti-laser face shield: To avoid skin damage due to laser radiation or spatter, you need a face shield that covers your face and neck from intense laser heat and wavelength. Some face shields also feature additional protection against UV radiation or debris.
- Laser welding-appropriate clothing: As per EN ISO 11611, it is advisable to use flame-resistant protective clothing that covers your entire body, like jackets, sleeves, and pants. You may also augment protective clothing against heat and energy that complies with EN ISO 11612, which indicates standards for flame-resistant materials used in industrial applications.
- Mask: For fine particles and residue, respiratory masks (FFP2 or FFP3) are recommended. This is highly suggested if you are working with chromium, nickel, or other heavy metals. You may also consider those with activated carbon filters for enhanced gas protection.
What Are the Principles of Laser Welding?
In a nutshell, laser welding is a process that fuses metals via three processes – energy absorption, melting, and solidification.
- Energy Absorption: The metallic workpieces will absorb the energy contained by the laser beam applied to their surface. A cleaner or smoother surface are more efficient in terms of energy absorption, while those with coatings or filled with contaminants can reflect or scatter the laser beam.
- Melting: As metals absorb the beam’s heat and energy, heat accumulation happens. The material’s temperature will eventually exceed its melting point.
- Solidification: After melting, the material cools and solidifies to form the weld. The cooling rate depends on factors such as laser power, welding speed, and material thermal conductivity. Proper solidification ensures a strong metallurgical bond and minimizes defects like porosity or cracking.
Denaliweld Helps You Achieve All Essential Laser Welding Requirements
As a leading global provider of cutting-edge laser welding solutions, Denaliweld is committed to providing industries with high-performing laser welding machines that meet performance and safety standards. Our standards-ready products are engineered with absolute precision, intuitive controls, and maximum safety to help operators achieve their desired weld quality and durability.