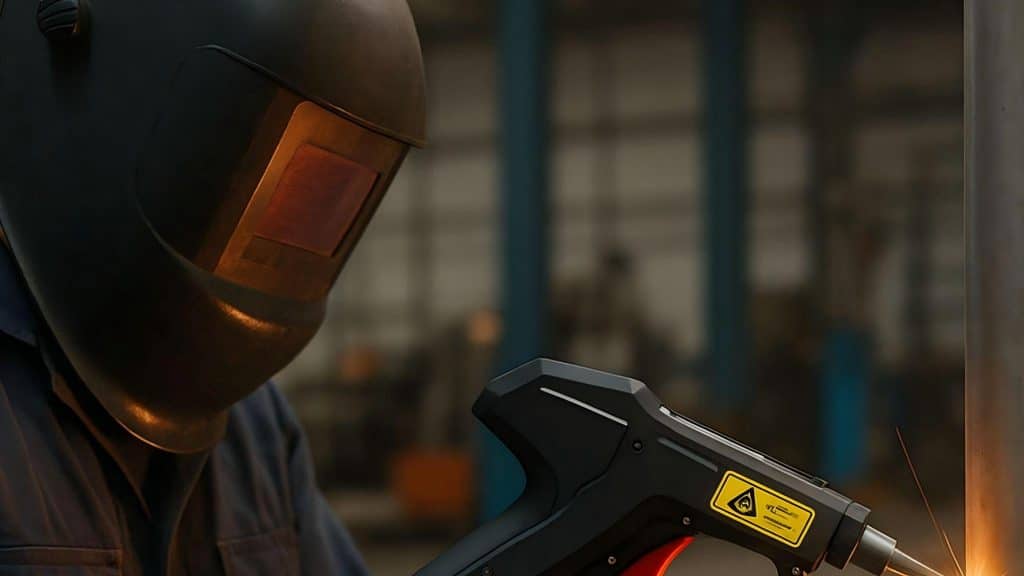
Every welder hates them—those unsightly splotches of molten metal that form around the weld. They look unappealing and often signal poor weld quality. We refer to them as weld spatter or “dingleberries”.
It is normal to spot some weld splatter around a joint, especially those made by traditional welding techniques (e.g. MIG or TIG). However, excessive presence of weld spatter can compromise weld strength and quality. They can also extend post-welding cleanup time or ruin the overall look of the product.
To avoid welding spatter, you must understand what causes it first. In this article, we discuss why spatter in welding forms and how to prevent it.
What Causes Spatter in Welding?
In a nutshell, weld spatter forms due to some faulty welding practices. It can be due to a wrong welding approach or negligence with the equipment or workpieces involved.
1. Incorrect Welding Parameters
Inaccurate or non-optimal welding parameters often cause spatter. For instance, extremely high amperage can cause weld spatter because it heats the material rapidly at low concentration, thereby causing expulsion of molten metal. Similarly, low voltage often forms weld spatter because of the repeated short-circuiting of the wire in the weld pool, which can cause small explosions on the wire’s tip.
2. Contaminated Workpieces
If impurities such as dirt, oil, rust, and other contaminants are present in high quantities in the workpieces, weld spatter is likely to form. These contaminants burn or vaporize upon application of heat which leads to ejection of molten metal from the weld pool.
3. Improper Shielding Gas Selection
Shielding gas serves as the weld pool’s protective barrier against external contamination. Incorrect shielding gas or insufficient flow rate can disrupt the weld arc and cause spatter.
Most metals use Carbon Dioxide, Argon, or a mix of the two as shielding gas because they are effective in minimizing weld spatter formation.
4. Worn or Incompatible Consumables
Using worn electrodes or wires often results in weld spatter. Their worn tip causes erratic wire feed, make the arc unstable, and enable the accumulation of molten globules on the nozzle.
Similarly, a consumable that is incompatible with the material can disrupt the welding arc and result in a messy transfer of molten metal.
How to Avoid Spatter in Welding: 10 Proven Tips
Once you understand the root cause of spatter in your welding projects, you can now address them using our actionable tactics below.
Optimize Welding Parameters
Welding parameters such as amperage (current), voltage, and speed of wire feed must be adjusted according to the material type and thickness.
In general, current and voltage must be within a “Goldilocks zone” – neither too high nor too low to ensure that the wire burns back in a controlled fashion and the arc remains stable.
Here is an example. A mild steel used in MIG welding often requires 18 to 22 volts and 100 to 200 amps to minimize spatter in the weld pool.
Moreover, you need to ensure that the wire feed speed is consistent with the recommended rate in the machine’s user manual. Optimal speed results in a regular metal transfer rate, which prevents weld spatter.
Clean the Workpiece Thoroughly
Prior to the welding process, the workpieces must be degreased of surface contaminants like oil, dirt, mill scale, and grease to ensure a clean weld. Even if they appear clean, some residue might still be present and affect weld quality.
Apply a solvent or degreaser such as acetone or isopropyl alcohol to a clean rag and use it to wipe the surfaces thoroughly. To remove rust or mill scale, an emery cloth or sandpaper can be used.
Select Appropriate Shielding Gas
To pick the correct shielding gas, you must consider the following:
- Welding process to be applied: For MIG welding, an inert gas like Argon or helium works. Active gases like CO2are also a good choice. For TIG welding, pure Argon or a mixture of Argon and Helium is used.
- Material type: Argon and Helium are commonly applied to non-ferrous metals like Aluminum and Titanium. Active gases like CO2are often used on ferrous metals like steel and stainless steel.
- Material thickness: The shielding gas must be compatible to the heat requirement of the workpieces based on its material thickness. For instance, thick materials which are over 5-mm thick use active gases like O2 or CO2.
Maintain Equipment and Consumables
Every welding machine requires regular maintenance and inspection to ensure optimal performance. Any worn parts need immediate replacement and clogs in the cooling system must be removed for proper ventilation.
Similarly, consumables need to be free from oxidation or rust to avoid impurities in the weld that can cause spatter. They must be stored in a dry and clean area to prevent rusting or contamination.
Use Anti-Spatter Products
Many anti-spatter products, such as gels and sprays, are available in the market. You can apply them to the metal’s surfaces or electrodes to keep spatter from touching them.
Make sure to choose anti-spatter products that are non-flammable and non-toxic, as well as compatible with the material type of your workpieces.
Implement Proper Welding Techniques
A skilled welder produces less spatter because they know the proper welding techniques. Here are some basic reminders to ensure you are doing the “right” approach.
- Do not weave the welding gun or torch excessively.
- For TIG welding, keep the torch at around a 15-20 degree angle from the workpiece.
- For MIG welding, keep the gun at around 5-15 degrees from vertical.
- Use the correct joint position (e.g. butt or corner joints) for your welding style.
- Position yourself and the workpieces comfortably to maintain a steady hand and consistent technique.
Consider Pulsed MIG Welding
In Pulsed MIG Welding, the machine’s pulsing action transfers the molten wire to weld puddle via a series of controlled, tiny droplets. This prevents contact of the wire to the puddle which often causes short circuit and spatter formation.
Choose the Right Filler Wire
A high-quality solid filler wire (usually metal-cored) is designed to minimize weld spatter. Avoid cheap filler materials with low-quality rods since they are usually unweldable or result in poor weld quality.
Ensure Proper Grounding
Proper grounding ensures a stable electrical connection between the welding equipment and the workpiece. One common way to achieve this is to attach a ground clamp directly to the metal to establish a direct electric path. If attachment is not feasible, you can use a designated grounding point on the welding table.
Invest in Advanced Welding Equipment
Most old-school welding techniques are prone to weld spatter because they often rely on bare electrodes or contaminated filler materials.
Laser welding and other advanced welding methods can ensure maximum spatter reduction because of their high-level precision, optimal heat input, controlled penetration, and versatility to various material types.
The Role of Advanced Welding Equipment in Spatter Reduction
The best way to prevent weld spatter is to invest in leading-edge equipment designed for modern welding techniques, such as laser welding. Denaliweld offers laser welding solutions engineered for optimal weld quality and zero spatter.
Denaliweld Jet 1000: Lightweight and versatile laser welding machine with state-of-the-art patented CUAL Mosaic Laser Source that ensures continuous, reliable, and controlled performance across a wide temperature range of -10℃ to 45℃ (10℉ to 110℉).
Denaliweld Air-Cooled Laser Welding Machine: An automation-ready laser welding machine with three-in-one capabilities (Welding, Cleaning, and Seam Cleaning). It is also Integrated with 100% U.S.-manufactured chips to ensure exceptional performance and long-term stability. And for consistent performance in extreme conditions, the machine is installed with an independent air-cooled design.
Denaliweld Water-Cooled Laser Welding Machine: Operated with cutting-edge chips for optimal performance and easy control. Offers stable and reliable performance in extreme conditions with its independent water-cooling system.
Wrap Up: Achieve High-Quality Weld and Minimal Weld Spatter
With the use of clean and high-quality workpieces, appropriate shielding gas, and correct welding practices, it is possible to reduce weld spatter and achieve robust welds.
But to achieve minimal to zero weld spatter, it is crucial to invest in high-quality welding equipment. Denaliweld manufactures innovative laser welding machines designed by top engineers and laser industry professionals. Our in-house sophisticated design features a sophisticated control system and power source for optimal welding speed and efficiency. Visit Denaliweld today.