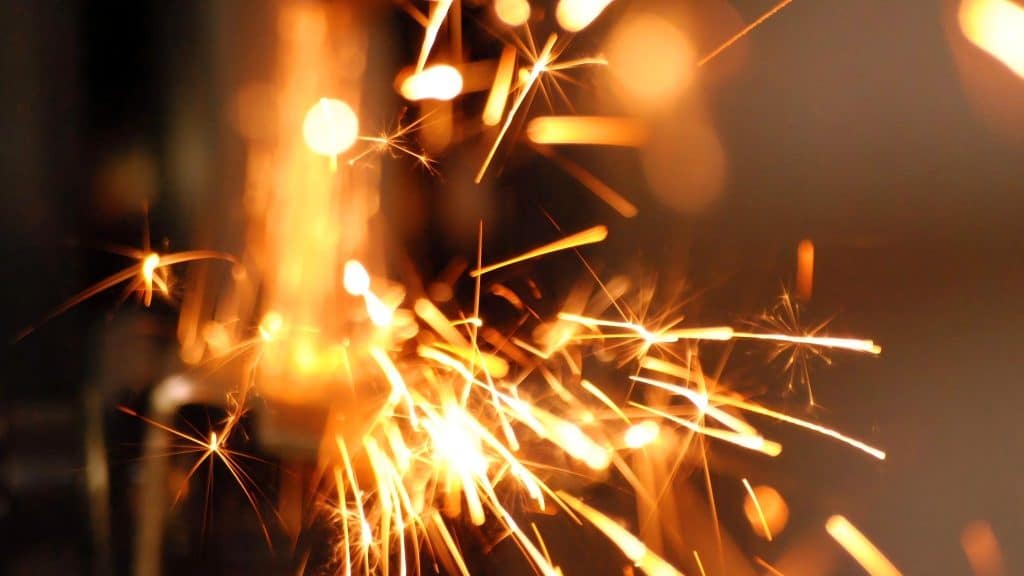
Fast, reliable, and efficient – some of the reasons why most manufacturers shifted to laser welding. This fast-growing technology can level up the firm’s turnaround time and significantly reduce its operating costs.
However, laser welding needs to satisfy stringent measures to achieve a high-quality weld with sufficient tolerance against stressors and common contaminants. Several international standards are in place to help manufacturers operate laser welding in a safe, efficient, and effective fashion.
Read on and recognize laser welding standards for various industries.
What Is the ISO Standard for Laser Beam Welding?
ISO 15609-4 is an international standard that formulates laser welding’s WPS (Welding Procedure Standards). This document presents a uniform welding approach for coherent and effective communication among manufacturers, inspectors, and regulators. With this unified specification, operators can document and execute laser welding in a systemized and standardized fashion.
There is also ISO 13919 which aims to complement ISO 15609-4 and highlights certain conditions for optimal weld quality and tolerance. Manufacturers use these guidelines to achieve optimal structural integrity, desirable joint geometry, and project-appropriate beam power.
For beam power and focus, ISO 15609-4 has certain provisions for critical laser welding aspects. For instance, manufacturers must provide detailed documentation of the laser’s power settings, particularly peak power and average power for various material types. This serves as the operator’s record-keeping of desirable laser input for efficient heat application that minimizes material degradation and defects.
Regarding weld joint geometry, this international standard reiterates the significance of proper material preparation and alignment to achieve a high-quality and clean weld. As the laser’s energy is highly concentrated, any gaps or misalignments can cause surface irregularities that may result in incomplete fusion of workpieces dominated by porous areas. As ISO 15609-4 standardizes joint geometry, laser welding becomes a predictive endeavor with low error risks.
Now consider laser process parameters, such as welding speed and shielding gas. These factors can affect weld’s strength and appearance if misconfigured. Poor material penetration and overheating usually stem from the use of incorrect speed or improper shielding gas flow. Metal oxidation and contamination might also happen, even with the slightest deviations in the optimal welding configuration.
Are There Standard-Compliant Modern Systems Available?
Compliance to strict international standards adds a burden to an operator’s job. For this reason, most laser welding solutions nowadays are engineered based on prevailing international standards.
Consider Denaliweld’s JET 1000, which is built to operate within strict international tolerances. This machine is a compact, lightweight, and versatile laser welding solution that works with absolute precision and portability. It features a patented CUAL Mosaic Laser Source that offers a reliable continuous operation in a wide temperature range of -10°C to 40°C (14°F to 104°F) for consistent performance in diverse environments. Furthermore, JET 1000 does not require an experienced welder to operate as the system is designed for quick learning.
What Are the Safety Requirements for Laser Welding?
The standards mentioned earlier focus on weld quality and structural integrity. Now, let us discuss some prominent safety international standards in place for laser welding.
ANSI Z136.1 lays out comprehensive guidelines and procedures for the safe utilization of lasers, including laser safety classifications. For instance, this standard classifies laser welding use under normal conditions in Class 1, while those that require application of high-risk lasers are classified as Class 4. This classification system also enumerates appropriate safety precautions and protective equipment when working with laser welding solutions.
Here’s an example, when a laser welding operation is classified as Class 4, the project is considered hazardous, which is capable of causing skin burns, eye injuries, and even material ignition.
Moreover, ANSI Z136.1 mandates the designation of Laser Controlled Areas when a laser welding system comes with significant safety risks. These zones must be clearly marked with warning signs and restricted to trained personnel. Access controls, such as interlocked doors or barriers, must be in place to prevent unauthorized entry.
Whether you are working on a Class 1 or Class 4 project, you need a laser welding machine that is sufficiently compact and versatile to ensure everyone’s safety. One example is Denaliweld’s Air-Cooled Laser Welding Machine, which simplifies operator training while complying with high safety requirements.
Denaliweld’s Air-cooled laser welding machine comes with built-in safety settings that provide enhanced protection for both users and observers for a safer working environment. Intuitive power options are available to help operators maintain a safe range of heat and power input during their welding operation.
What Are the Tolerances for Laser Welding?
In laser welding, tolerance pertains to allowable deviations or discrepancies in the dimensions, alignment, or processing laser parameters without compromising weld quality or functionality. Tolerance also defines the acceptable limits for deviations in factors like joint fit-up, material thickness, weld penetration, and positioning of the laser beam.
For instance, ISO 13919-1 discusses tolerance levels for steel, which outlines permissible levels of imperfections such as cracks, porosity, and undercut, depending on the welding class (B for high quality, C for moderate quality). On the other hand, ISO 13919-2 applies similar principles to aluminum and its alloys. This document details tolerances for weld defects like incomplete fusion or excessive penetration.
Tight tolerances are vital in industries such as electronics and aerospace, where precision and reliability are imperative. In electronics, micro-scale components demand welds with minimal heat-affected zones to minimize damage to sensitive materials. In aerospace, welds must withstand extreme mechanical stresses and environmental conditions. There is no room for minor defects, as even the smallest ones can be fatal.
Denaliweld Upholds Strict Laser Welding Standards for Optimal Weld Quality
Laser welding is primarily known for its agility and power. But to leverage its full potential, operators must invest in a laser welding solution that complies with performance and safety standards.
Check out Denaliweld’s laser welding solutions. We are a top-notch global manufacturer of laser welding machines made to adhere to prevailing welding international standards. We are committed to providing welding operators with safe mechanisms and controls to produce top-quality welds for any industrial application.