As stainless steel products become more common, people want better welding for both accuracy and looks. Traditional welding often lacks precision, leading to unreliable quality that does not meet requirements. Laser welding is better than traditional methods in quality, precision, efficiency, and automation. It can significantly improve welding efficiency.
High-power laser equipment is becoming more popular, leading to rapid advancements in laser welding technology in the industrial sector. So, what is laser welding? How is its effect? Laser welding can weld how thick the material?
How thick can a hand-held laser welder weld?
The ability of a laser welding machine to weld thickness is affected by a number of factors. In general, the power of the laser welding machine is usually the main determinant of the thickness of the weld, in addition to the material properties, the form of the weld and many other factors.
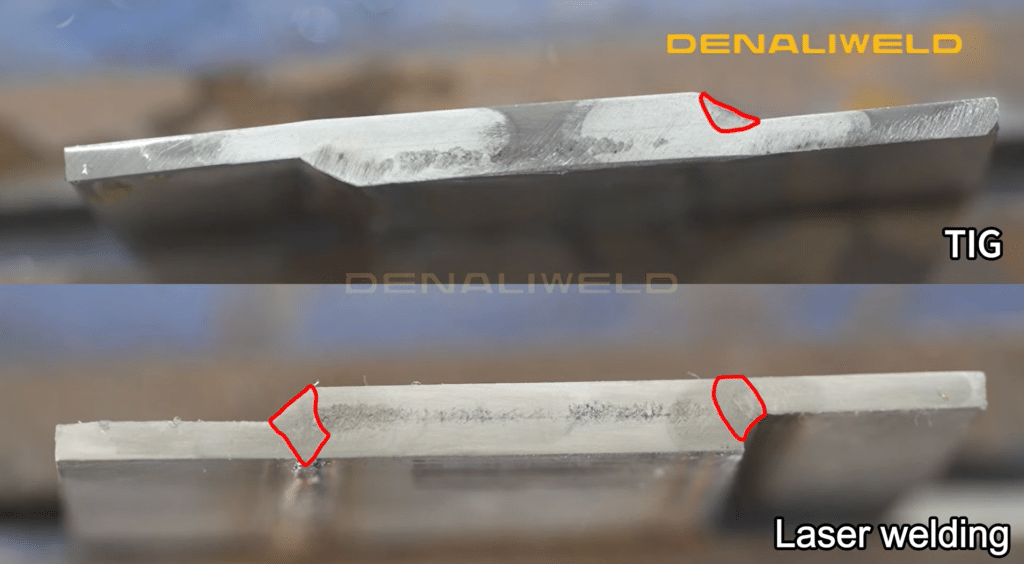
The thickness of the weld determines how much power should be used, i.e., the greater the thickness of the workpiece to be welded, the greater the power of the selected laser welding machine should tend to be.
1、1000W laser welding machine: suitable for welding plates with thickness of 3mm and below.
2、2000W laser welding machine: suitable for welding plates with thickness of 5mm and below.
3、3000W laser welding machine: suitable for welding plates with thickness of 8mm and below.
It should be noted that different welding materials have different degrees of laser absorption, welding needs to be flexible according to the welding material to adjust the power size to meet the welding thickness.
Welding process parameter table (wire feeding) | |||||||
Material | THickness | Power | Freq | Focus | Wobble Size | Wobble Size | Melting Depth |
SS | 1.0mm | 600W | 1000HZ | -1.5 | 2.0mm | 100HZ | 1.0mm |
1.5mm | 800W | 1000HZ | -1.5 | 2.0mm | 80HZ | 1.5mm | |
2.0mm | 1000W | 1000HZ | -2 | 2.0mm | 70HZ | 2.0mm | |
3.0mm | 1500W | 1000HZ | -2 | 2.5mm | 60HZ | 2.5mm | |
4.0mm | 2000W | 1000HZ | -2 | 3.0mm | 50HZ | 3.0mm | |
5.0mm | 2400W | 1000HZ | -3 | 3.0mm | 40HZ | 4.0mm | |
6.0mm | 2800W | 1000HZ | -3 | 3.0mm | 30HZ | 5.0mm | |
AL(5 series) | 1.0mm | 600W | 1000HZ | 0 | 2.0mm | 80HZ | 1.0mm |
2.0mm | 1000W | 1000HZ | 0 | 2.5mm | 70HZ | 2.0mm | |
3.0mm | 1500W | 1000HZ | -1 | 2.5mm | 60HZ | 2.5mm | |
4.0mm | 2000W | 1000HZ | -2 | 3.0mm | 60HZ | 3.0mm | |
5.0mm | 2400W | 1000HZ | -3 | 3.0mm | 50HZ | 4.0mm | |
CS | 1.0mm | 600W | 1000HZ | +2 | 2.0mm | 80HZ | 1.0mm |
2.0mm | 1000W | 1000HZ | +2 | 2.0mm | 80HZ | 2.0mm | |
3.0mm | 1500W | 1000HZ | +2 | 2.5mm | 60HZ | 2.5mm | |
4.0mm | 2000W | 1000HZ | +2 | 3.0mm | 50HZ | 3.0mm | |
5.0mm | 2400W | 1000HZ | +3 | 3.0mm | 40HZ | 4.0mm | |
6.0mm | 2600W | 1000HZ | +4 | 3.0mm | 40HZ | 5.0mm | |
8.0mm | 2800W | 1000HZ | +4 | 3.0mm | 30HZ | 6.0mm |
In our practical tests, laser welding is significantly ahead of tig welding (without beveling) in terms of depth of weld and welding speed.
A video can be seen in the tig welding transverse heat affected zone is very large, giving a person in the intuitive feeling of the depth of fusion is very high, but in the cutting weld etching will find that the tig welding depth of fusion can only reach about one-third of the laser welding!
For partial penetration welds, the minimum penetration into the negative should be between 20% and 50% for thinner materials and 0.5 mm for thicker materials to ensure repeatable fusion
Stainless steel, carbon steel, aluminum and its alloy materials are some of the most common materials in production. Among them, the melting point of aluminum is lower than many metals, but it has a certain degree of reflectivity, resulting in the laser energy will be partially reflected out of the melting effect, which is the reason why the welding power of aluminum is greater than that of other materials.
In the use of laser welding machine, welding speed is also an important factor in determining the welding effect
Weld quality:If the welding speed is too slow, the thinner the workpiece may be welded through, the thicker the workpiece may lead to the depth of fusion is too deep, the strength of the weld seam is too high, and there may be pores and cracks; on the contrary, the welding speed is too fast which may lead to the shallow depth of fusion, the strength of the weld seam is weaker but the probability of the appearance of pores and cracks is lower.
Weld shape:The slower the welding speed, the wider and deeper the weld channel, the faster the welding speed, the narrower and shallower the weld channel.
Work efficiency:The right welding speed can improve productivity and save labor and time costs, but too slow welding speed will lead to low work efficiency and low production capacity, thus failing to complete the workload.
Therefore, when working with the laser welding machine, adjusting the welding speed and other parameters according to the instruction manual according to the material and thickness of the welded workpiece will greatly help to improve the work efficiency.
Advantages And Disadvantages of Laser Welding
Nowadays, laser welding machines have been maturely applied in many fields, and laser welding machines have some unique advantages compared with traditional welding equipment.
1, Welding speed, low power consumption, can realize continuous high-speed welding, improve welding efficiency;
2, Can realize precision welding, weld seam beautiful, can be applied to high-precision, high-demand occasions;
3、Simple operation, non-professionals can also realize professional welding, without expensive training costs;
4、Small heat-affected zone, small thermal deformation, can reduce the thermal impact on the surrounding materials.
5, High degree of automation of laser welding, with collaborative robots, you can control the welding process through the computer, to mention the production efficiency;
6, Can weld a variety of materials, stainless steel, carbon steel, iron, galvanized sheet, aluminum and its alloys and other materials can be welded;
7, Relatively low maintenance costs, low cost of replacement parts, Denali has a perfect after-sales service, no need to worry about after-sales problems;
Of course, laser welding machine also has certain disadvantages
Higher Price:Compared with the traditional welding machine, the price of laser welding machine is relatively high, so the initial investment will be relatively large;
Thickness:The laser welding machine has some limitations on the welding thickness, which is not very suitable for the welding of ultra-thick materials. learn more》
Laser Welding Applications
With its high precision, high efficiency and applicability to a wide range of materials, the laser welding machine has become an indispensable welding tool in the modern manufacturing industry, and is widely used in advertising lighting, sanitary ware industry, metal processing, automobile manufacturing, medical equipment, aerospace, electronics manufacturing and many other industries.
Practical application cases:
Sanitary industry: water pipe joints, reducer joints, tees, valves, shower welding;
Hardware industry: impeller, kettle, handle, etc., complex stamping parts, casting parts welding;
Automotive industry: engine cylinder gasket, hydraulic tappet seal welding, spark plug welding, filter welding.
Medical industry: medical apparatus, medical equipment, stainless steel seals, structural parts of the welding.
Electronic industry: solid state relay sealing break welding, connectors plug welding, cell phones, MP3 and other metal shell and structural parts of the welding;
Household hardware, kitchenware and sanitary ware, stainless steel door handles, electronic components, sensors, clocks and watches, precision machinery, communications, handicrafts and other industries, automotive hydraulic tappet and other high-strength industry product welding.
Precautions for use of laser welding machine
We can increase our efficiency by using a laser welding machine, but if it is not operated correctly, it can damage the machine in addition to affecting the welding effect of the machinery. Therefore, to ensure the safety of using a laser welding machine, there needs to be strict control over laser welding hazards, good engineering management, personal protection, and safety measures.
1.Before the start of welding must pay attention to safety measures, the user must wear professional laser protective glasses, protective clothing and gloves and other personal protective equipment, in order to avoid laser damage to the human body.
2.When welding, make sure the work space is set up and that everyone nearby is aware of the safety distance. Also, remove any combustible materials that may be present.
3. The user needs to operate in accordance with the operating instructions and related standards, and strictly follow the operating specifications in order to avoid accidents.
4. During the work period, handheld laser welding machine safety norms do not use the eyes to look directly at the laser beam, also do not let any part of the body contact the laser beam, so as not to cause injury.
5. Pay attention to keep the environment and handheld laser welding machine clean, the use of the process can not be directly on the ground welding head to prevent dust on it.
6. Equipment failure, first contact the laser welding machine manufacturers, seek technical help to solve the problem, in the absence of understanding the problem, do not disassemble and repair.
Learn more about what to look for in a laser welding machine